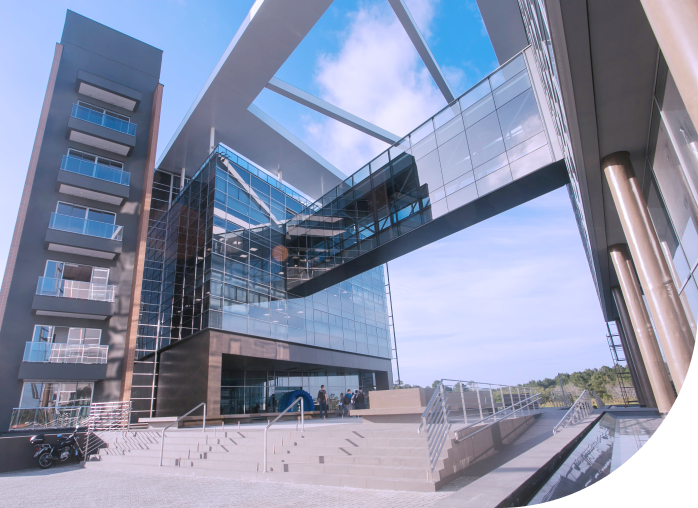
Transformation has always been part of our history.
We transform challenges into opportunities and develop solutions that drive businesses and change lives.
We move forward alongside those who believe in the power of change. We are ready to transform the present and shape the future with responsibility, strategic vision and the solidity of those who have been delivering technology solutions for over 30 years.
The time has come to transform once again: as a result of our evolution, the Group Softplan now it is reorganized into two distinct fronts, but aligned in purpose.
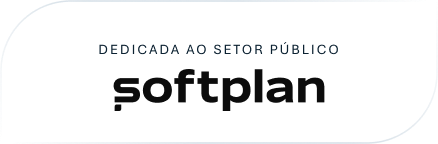
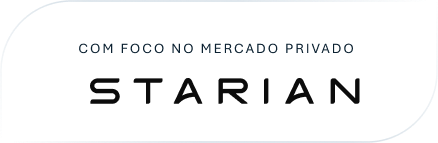
The transformation that begins now is
result of more than three decades of history
International
Welcome to our new phase:
More protagonism in what we deliver and more
intention in how we position ourselves.
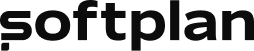
We are focused on digital transformation, with a clear objective: to develop software by finding intelligent solutions for the infrastructure and construction, digital processes and justice segments, bringing technology and integration to all areas of the Public Sector. We are a trusted advisor in technology for the sector, with an impeccable track record in reliability, compliance and reputation.
Learn more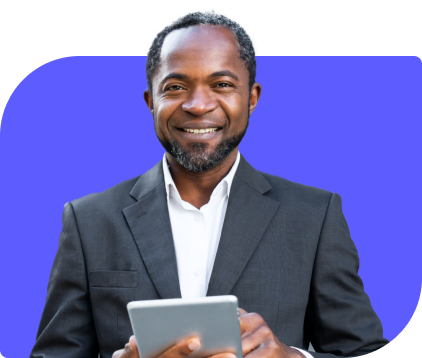

We develop and incorporate SaaS (Software as a Service) solutions as a growth engine and enabler of new business lines for the verticals in which we operate, such as the Construction Industry, Legal Intelligence and Operational Efficiency.
Learn more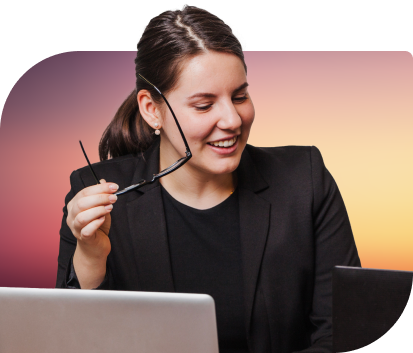
Discover the careers Softplan and Starian
Be part of the teams that transform challenges into real solutions and guide businesses towards the future.
Learn more